Enabling sustainable, efficient and safe heating and cooling with propane
Natural refrigerants are gaining importance in many commercial heating and cooling applications, as new environmental rules phase out the use of refrigerants with a high global warming potential (GWP). In Europe, in particular, the EU F-Gas Regulation will ban refrigerants with a GWP above 1500, and many expect the guidelines to become even stricter in the future. That’s why a growing number of system builders are turning to hydrocarbons like propane (R290). With a GWP of just 3, propane offers a future-proof refrigerant solution to meet the tough new rules coming tomorrow.
DATE 2023-11-28Simaka Energie- und Umwelttechnik GmbH, a German provider of thermal solutions, is one company that has been eager to show their customers the potential of working with propane as a refrigerant. Together with Alfa Laval, they have engineered a heat pump system for a Swiss supermarket chain, based around three Alfa Laval brazed plate heat exchangers; which are extra-large, have a very high capacity, and use R290 as a refrigerant. The result was an innovative heating and cooling solution that offers the best assurance of long-term sustainability, energy efficiency, and safe operation.
Installed Alfa Laval brazed plate heat exchangers in the heat pump. To the left; AC500 condenser, in the center; AC1000 evaporator, and to the right AC500 condenser.
Simaka’s mission is to develop customized systems for customers, which exceed requirements for thermal efficiency, GWP-levels and cost-effectiveness, ensuring future-proof peace of mind. Based in Argenbühl in Baden-Württemberg, Germany, they have been early adopters of natural refrigerants, designing innovative heat pumps for industrial heating and cooling for many years. The company is therefore uniquely situated to understand the demands of today’s market and the challenges involved for customers in switching to low-GWP alternatives.
In my view, the F-Gas Regulation represents the biggest departure related to refrigerant bans in the last 30 years,” explains Karsten Uitz, Managing Director at Simaka. “Until now, there was always a substitute in place that met all relevant safety criteria. As a refrigeration contractor today, however, you can’t get around flammable refrigerants like propane or R1234ze. You have to be able to handle them.”
At the forefront of natural refrigerants
Simaka is located just 50 kilometres from Germany’s border with Switzerland, a country that has led the way in implementing requirements for lower-GWP refrigerants. As a result, businesses operating in Switzerland consider it very likely that the future will bring even tougher sustainability targets.
These considerations were central to the major Swiss supermarket chain, who, in the summer of 2020, invited bids for a heat pump with constant cooling function. The customer’s specifications required a total output of 550 kW and, critically, the use of R290 as the main refrigerant. Given Simaka’s innovative focus on use of a natural refrigerant, Uitz and his team of process engineers were eager to accept the challenge – and beat out the competition.
Ensuring maximum efficiency is in every last detail
“Efficiency is Simaka’s passion, and we build systems that provide our customers with the best benefits down to the smallest details,” says Uitz. “We know that if a heat pump is not running at the intended efficiency level, there will be more electricity costs down the road, as well as higher CO2 emissions in the end. Ensuring our system would deliver the promised performance was thus a team effort with Alfa Laval, because I can 100% rely on them to optimally size and assemble the necessary components for us.”
For the Swiss supermarket chain, Simaka developed a heating and cooling system, which is connected via a large Alfa Laval AC1000 brazed plate heat exchanger to a hydraulic cooling circuit and two identical AC500 brazed plate heat exchangers connected to two separate hydraulic heating circuits. The AC500 brazed plate heat exchangers are used as condensers and each is filled with 30 kg of propane. Simaka designed the system with 50% redundancy to ensure that the system continues to provide half of the total capacity if one refrigerant circuit fails.
Additionally, having two separate condensers allows operators to run different condensing pressures, and hence temperatures in the two refrigeration circuits. For example, one circuit can operate at a lower discharge temperature enabled by a lower pressure resulting in greater thermal efficiency and thus energy efficiency.
Refrigerant Comparison by Simaka Energie-
und Umwelttechnik GmbH
Refrigerant | R290 (propane) | R134a (tetrafluoroethane) | R407c |
---|---|---|---|
GWP | 3 | 1430 | 1770 |
Evaporation temperature [°C] | -17 | -17 | -17 |
Condensation temperature [°C] | 46 | 46 | 46 |
Heating capacity [kW] | 585.5 | 389 | 572 |
Refrigerating capacity [kW] | 409.3 | 265.3 | 384.1 |
Electrical power consumption [kW] | 299.8 | 124.2 | 188.2 |
Current consumption [A] | 176.2 | 226.4 | 317.5 |
COP | 3.32 | 3.13 | 3.04 |
Unique designs to meet high requirements
The large AC1000 brazed plate heat exchangers are designed with a very small footprint, which has helped Simaka to take full advantage of R290’s good volumetric performance. As a result the high-capacity heat pump system they have engineered can deliver the required 550 kW within a compact, and thus cost-saving, design.
Thanks to Alfa Laval’s unique FlexFlow™ asymmetrical plate design and the fully customized Dynastatic™ integrated distribution system, the large AC1000 brazed plate heat exchangers ensure excellent refrigerant distribution, and at the same time achieving low pressure losses on the hydraulic cooling side. This reduces pump capacity requirements, which reduces the electrical energy consumption and that translates to even further reduced CO2 emissions. Additionally, the plate asymmetry guarantees the best thermal performance even at partial loads.
“With Alfa Laval, we always find the design know-how and experience needed to ensure the optimal heat exchangers for our systems,” Uitz says. “That’s true from the smallest capacities to the largest that we run, and includes details such as the oil return, as well as the very close temperature approach, so there is no compromise to efficiency. We came to this project with high requirements, and Alfa Laval has designed our large AC1000 brazed plate heat exchangers to meet them exactly."
Reliable performance with safety to match
The 60 kg of propane used in the system is far above the limit for operating without dedicated explosion protection. Safety was therefore a key consideration in the construction of the system and Simaka’s choice of components. This was another reason why they relied on such close cooperation with Alfa Laval.
Heat exchangers are the be-all and end-all when dealing with flammable refrigerants,” Uitz says. “The heat exchangers used have to be absolutely reliable, even in the long term. Here, too, Alfa Laval’s quality has never disappointed us. We have never had a single failure due to a leaking heat exchanger.”
The redundancy design once again offers a benefit, since it means that the amount of propane in a given refrigeration circuit is cut by half. Were the propane to escape, the system would immediately shut down, and an explosion-proof fan would blow it away. This can be done safely since the system is located on the supermarket roof, rather than inside the building, and Uitz recommends that any system of such a scale using flammable refrigerants should be installed outdoors for exactly this reason.
Heat pump type SIMATRON WP550SW, at Simaka Energie- und Umwelttechnik GmbH.
Successful results from a successful partnership
While many customers may still have safety concerns, Simaka is confident that propane and other hydrocarbons will continue to gain prevalence on the market within the medium-term. “In the long run, there will be no getting around flammable refrigerants,” Uitz concludes. “R290 allows the construction of compact, efficient systems due to its volumetric refrigeration capacity. This is reflected in the low CAPEX and OPEX for customers. At the same time, the low GWP guarantees it will continue to meet the requirements of legislation well beyond 2030.”
Given the success of the Swiss supermarket project, Uitz looks positively at the outlook for the future . “For us, this means many exciting projects in close partnership with Alfa Laval in the coming years,” he adds. “We are looking forward to them, as our professional collaboration has resulted in many great ideas, which we have been able to turn into perfect reality with the support of Alfa Laval’s comprehensive service.”
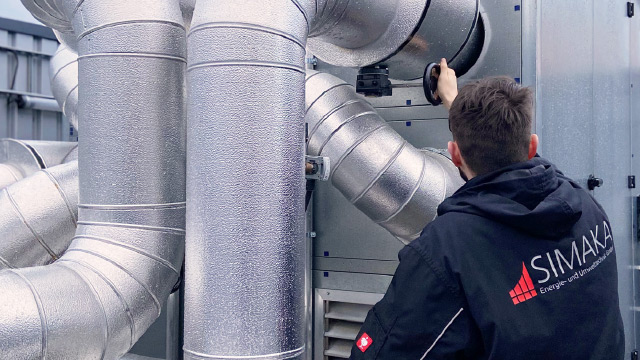
Download case story
Accelerating sustainable solutions
Together with our customers and our partners, Alfa Laval is accelerating the transition to more efficient, cleaner energy solutions and moving the circular economy forward.
Our deep industry knowledges enables us to optimize customer processes, overcome the toughest challenges, and continue making the world better every single day.
Alfa Laval copper-brazed plate heat exchangers are a compact, efficient and maintenance-free solution for heating, cooling, evaporation and condensing in numerous applications.
Brazed plate heat exchanger solutions